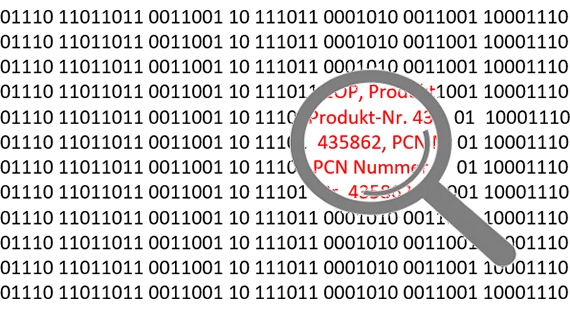
Bill of material analysis, cleansing & monitoring
Send us up to 1,000 manufacturer numbers (XPN) and the associated manufacturer names (XMN), which we will check for change for discontinuation and/or change notifications (so-called PCN notifications) without obligation for you. You will receive the result within 2 working days.
We check the cleansing of your master data for you to ensure an automated and therefore digital & secure reconciliation process. We are happy to have an informal chat with you about which data and how much should be cleansed.
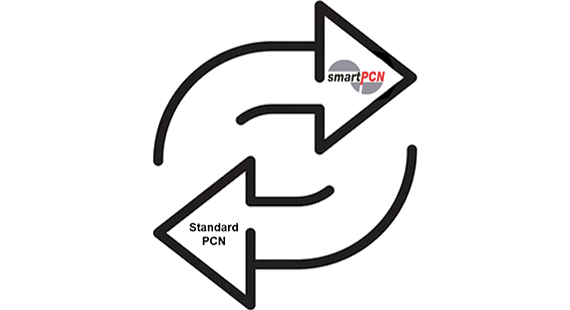
smartPCN format
A standard smartPCN does not contain any customer-specific data of the PCN recipient (such as your internal part numbers or order information). Via pcn.cockpit you will receive PCNs that you have sent to us even if there are no matches with your component data.
The conversion is usually done in such a way that the original PCNs/PDNs are evaluated and the contents specified in smartPCN 3.0/VDMA 24903 are entered into the database. Any missing information, such as the specific product numbers/part numbers, will be researched. The original PCN/PDN is saved as an attachment in the data set. In addition to smartPCNs that are generally accessible to all users, confidential smartPCNs that are only accessible to the customer in question are also stored.
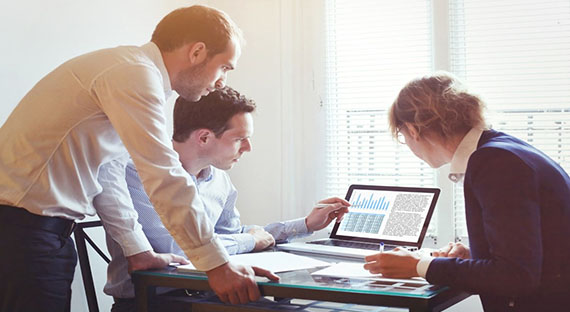
Complex spare parts for technical equipment such as controls, motors, or sensors are subject to technical change and have a limited market availability. For technical equipment with a long service life, the risk of spare parts being discontinued and no longer available increases disproportionately over time.
Neither users nor manufacturers can predict when the part is discontinued
We can help you identify the risk factors in your company and derive appropriate actions from these identified risks.
You move away from reactive OM towards proactive and strategic obsolescence management.
Look through and evaluate existing structures and bring about the optimum level of automation based on the available resources. This is done taking into account existing standards (e.g. VDMA 24903, IEC 62402…) and directives such as REACH, RoHS, SCIP…. as well as your management specifications.
We are a leading member of the COGD (Component Obsolescence Group Deutschland e.V.) and Dr. Heinbach serves as honorary president. We are also a member of the British umbrella organization of the IIOM (International Institute of Obsolescence Management). We are also involved in the IEC/IECQ, the DKE and the VDMA, which enables our customers to always act in compliance with the current regulations.
The aim is to reduce the workload for you and your employees and enhance your security. We have the products to implement this and many years of expertise.
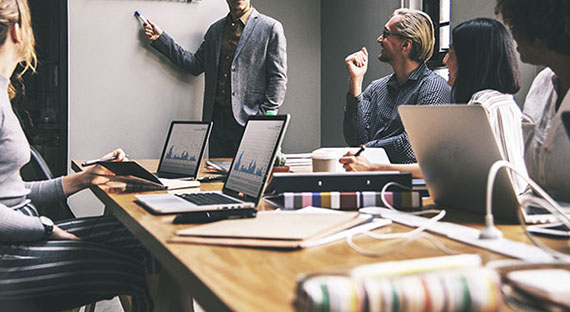
We train you in the use of our software products and noticeably reduce the workload for your day-to-day business.
We host mostly in-person on-site or online meetings where we explain to you how our software products work and give your exercises. We continue to provide your with competent advice after the training sessions.
We also offer workshops on the listed topics in the field of obsolescence management. The workshops we hold at your company premises or, usually, as part of our annual events, allow you to contribute your knowledge and benefit from the extensive package of topics we introduce there. We make the workshop materials available to you after the event, which you can use as a reference work and pass on to your colleagues.